When you conduct an analysis, you perform a detailed examination of a particular thing. The details gathered in an analysis are then used as a subject or basis for a discussion or for interpretation. Performing an analysis is like conducting an investigation where the main causes of something are identified in order to find ways for improvement and avoid waste or failure.
Featured in this article is a specific type of analysis called product cost analysis. Here we will define what it is, its uses and other basic information about it. We have also prepared useful samples and templates that you may download an use as reference. Check them out below!
Simple Product Cost Analysis Template
Sample Product Cost Analysis
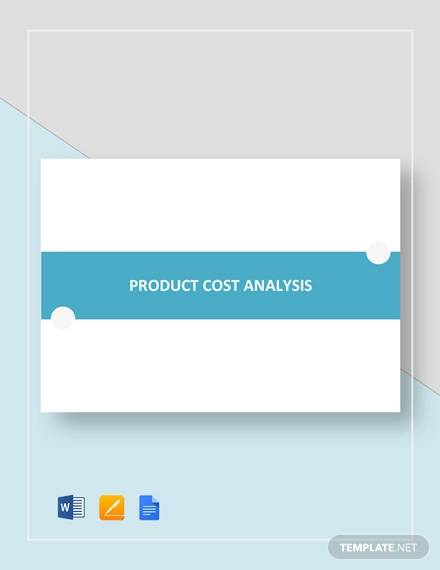
Production Cost Benefit Analysis
Product Development Process Cost Analysis
Production Cost Analysis Example
Product Cost Analysis During Pre-Development
Product Cost Analysis Template
What Is a Product Cost Analysis?
Everything that is done in a business costs something and that includes production. Production costs refer to the costs or expenses incurred by a business or company in manufacturing a product or a proving quality service. You can’t really identify it as a material cost alone as it includes a variety of expenses, like labor, supplies, overhead, consumable manufacturing, raw materials and many more. It doesn’t stop their, government imposed taxes and royalties also contribute to the expenses or costs that a company or business need to cover.
In production, costs can be categorized as direct and indirect costs. Direct costs refer to the costs of the materials and labor required to actually produce the final product, which includes plastic and metal materials for manufacturing, and the costs paid for the labor rendered. Indirect costs on the other hand are more on other necessities that are required for production, like rent of the facilities or equipment, administrative salaries, overhead and other utility expenses.
A production cost analysis is used to drive up the unit costs for product pricing. The cost of production is itemized into various components to effectively reduce the cost for the manufacturing of products or provision of services without sacrificing the quality of the products or services. With that being said, businesses will be able to gain more and spend less, which is a good business opportunity for them to take advantage of.
The cost of production can be calculated using the formula below:
Product unit cost = (Total costs for direct labor + Total costs for direct materials + Consumable manufacturing supplies + Total costs allocated for overhead) ÷ Total number of units
If a product has not yet been sold, then it can be recorded as part of the inventory asset and as soon as it is sold, it is going to be charged to the costs of goods sold. It then appears as an expense in the income statement of the company or the business. Product costs also makes its appearance in the financial statements of the company or business.
There are a lot of things that can find out about analysis by checking out other related articles, like Cost Breakdown Analysis Templates, Event Cost Analysis Templates, and Cost Benefit Analysis Templates.
What Are the Types of Costs?
There are mainly six types of costs that are involved in production and they are labor costs, material costs, conversion costs, logistics costs, subcontracting costs, and overhead costs. Each of these costs are essential for the business and its processes. Let us check out each of these types below.
Labor Costs
Labor costs refer to the amount of money used to pay for the people who worked in the manufacturing of the products or those who provided the actual service to clients. It is a direct labor costs and is the most common starting point for manipulation as in cost reduction because it is easily identified. labor hours and the rate of labor are included in labor costs.
Material Costs
This cost refers to all of the materials bought by the company or business, regardless if they are raw materials, manufacturing supplies or some parts or components for production. Insurance expenses and frieght are also accounted as part of material costs of a business or company.
Conversion Costs
Included in conversion costs are manufacturing costs, costs of utilities and maintenance costs. These costs are derived from the process of converting the raw materials into the actual product or finished product.
Logistics Costs
There are a number of factors that affects this cost and these factors are transportation costs, custom clearance costs, warehousing costs and distribution costs for the products. There are limitations to the transport of the products form one location to another and the corresponding costs vary based on the distance traveled, the laws governing the import of products of a country.
Subcontracting Costs
Subcontracting costs are direct costs to a business and they refer to all of the expenses related to subcontracting, which includes outsourcing of certain obligation through a contract with another party or a third party.
Overhead Costs
Overhead costs belong to the so-called hidden costs as they cannot be directly allocated to a particular cost unit, although they are ongoing business expenses. They do not directly create profit for the business, but they offer a useful contribution in the activities of the company or business that are ongoing. For example, company cars don’t really generate profit or income for the company but they are very useful when employees need to attend important meetings outside of the office. This allows them to arrive on meeting and other important business transactions on time.
Other related articles include Incident Root Cause Analysis Template, Simple SWOT Analysis Template, and Worksheet Competitor Analysis Templates.
Monthly Cost Breakdown Analysis Template
Product Costing Template
Printable Cost Benefit Analysis Template
Cost Benefit Analysis Template
Blank Event Cost Analysis Template
Advantages of Analysis Templates
Product cost analysis templates are tools used in creating a product cost analysis output or report. They are ready made documents complete with the standard details needed in a product cost analysis. The document is completed by supplying specific and actual information or data to it. Here are some of the advantages offered by a analysis templates.
- Analysis templates are tools that can be easily used as they do not require any special skills or abilities to be completed.
- They make the task of conducting the analysis easy and convenient. With the template ready, findings can be easily recorded in the template which eliminates the need for drafts and other scratch paper.
- Documentation and recording is made easier with the use of the templates.
- Templates eliminate the need to recreate the same document every time it is needed. This not only saves the user time, but it also allows them to use their brain power and other resources and more important things.
- Templates come in different varieties and file formats to make sure that everyone can find the actual template that they need or one that is exactly what they need.
- A lot of templates are available online and they are mostly for free or for a small fee and there is actually nor forcing you to buy one if you don’t want to.
- You can have the templates edited and printed. This means you can make the necessary changes to the file and have it printed afterwards. templates are also available in different file formats.
If you don’t find templates useful and beneficial with all those advantages listed above, then I don’t know what would. You may also check out titles, like Checklist Trend Analysis Templates, Medicare Coverage Analysis Templates, and Advertising SWOT Analysis Templates.
Key Takeaways
- Production cost analysis is a type of analysis that is done to systematically items all of the costs or expenses involved in the production of good or provision of services into components. This way they costs can be effectively reduced without having to sacrificed the quality of the products and the services offered.
- Production costs are divided into direct costs and indirect costs. Direct costs are costs from purchasing the materials needed in to make the final product, while indirect costs are those spend on the things needed to carry out the production.
- There are six types of costs that businesses or companies spend on and they are labor costs, material costs, conversion costs, logistics costs, subcontracting costs, and overhead costs. The cost that is most common and is used as the starting point for cost cutting is the labor cost due to its identifiability.
- Product cost analysis have templates that makes the entire process of easy and convenient to do. It offers a lot of advantages to is user such as being able to save time and brain power, ease of use, having reliable contents, and provides a convenient way to record and document the data gathering process.
We hope that you were able to learn about product cost analysis templates in this article. If you are interested to know more or get hold of useful templates, we have a variety of articles that you can choose from. Some examples are Investment Analysis Templates, Needs Analysis Templates, and Company Analysis Templates.
Related Posts
FREE 10+ Fishbone Root Cause Analysis Samples in PDF
FREE 11+ Cost Volume Profit Analysis Samples & Templates in PDF | MS Word
FREE 6+ Corporate Portfolio Analysis Samples in PDF
FREE 10+ Fault Tree Analysis Samples in PDF
FREE 10+ Comp Analysis Samples in PDF
FREE 10+ Fishbone Analysis Samples in PDF
FREE 10+ Individual Swot Analysis Samples in PDF
FREE 10+ 5 Year Analysis Samples in PDF
FREE 10+ Benefit Costs Analysis Samples in PDF
FREE 10+ Job Hazard Analysis Samples in PDF
FREE 10+ Primary Source Analysis Samples in PDF
FREE 10+ Critical Path Analysis Samples in PDF
FREE 10+ Competition Analysis Samples in PDF
FREE 10+ Activity Hazard Analysis Samples in PDF
FREE 10+ Risk Benefit Analysis Samples in PDF