The manufacturing sector thrives on precision and planning. Integral to this is a well-conceived Action Plan, which when paired with a stellar manufacturing template, can drive unparalleled efficiency and productivity. If you’re on the hunt for a transformative approach that harmonizes every aspect of your production process, our Sample Manufacturing Template is your golden ticket. Step into a realm of optimized workflows and strategic foresight with our comprehensive guide.
1. Sample Budget Manufacturing Template
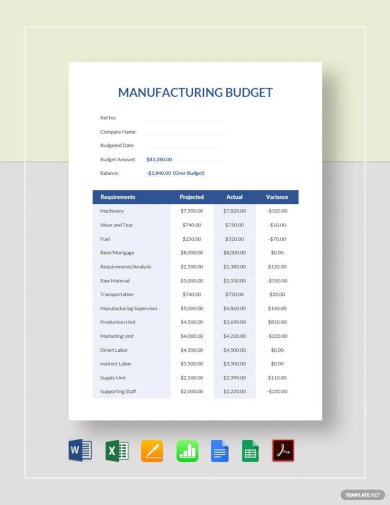
2. Sample Manufacturing Work Instruction Template
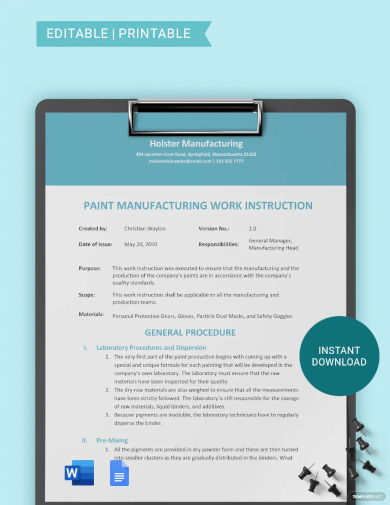
3. Sample Manufacturing Standard Operating procedure Template
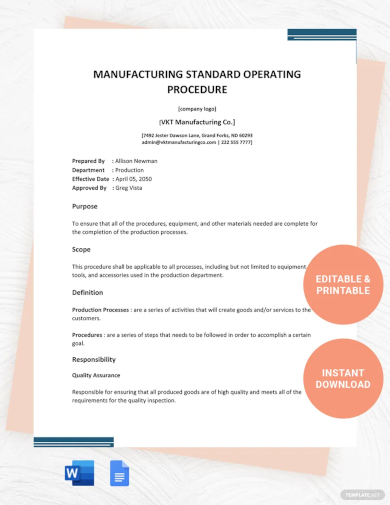
4. Sample Manufacturing Business Continuity Plan Template
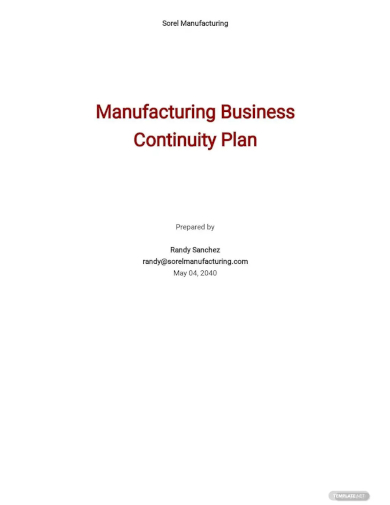
5. Sample Manufacturing Project Report Template
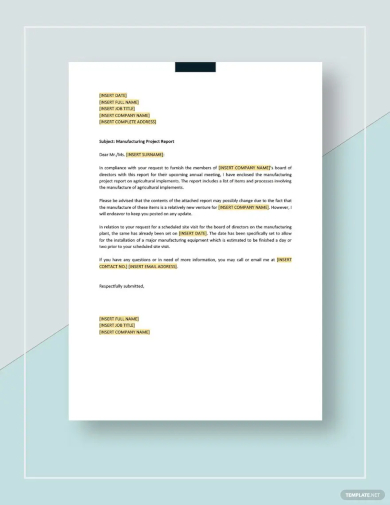
What is a Manufacturing Template?
A manufacturing template can be thought of as a blueprint or guideline used within the manufacturing industry to standardize processes, ensure consistency, and improve efficiency. Given the complexity of modern manufacturing operations, having standardized tools and frameworks like templates becomes paramount. These tools not only simplify the entire production process but also help in achieving consistent and high-quality output.
The Role of a Manufacturing Template
Standardization: One of the primary purposes of a manufacturing template is to ensure standardization across production cycles. Different batches of products, even when produced weeks or months apart, should have consistent quality and specifications. By following a set template, manufacturers can ensure that every product is made to the same standard, reducing variations and defects.
Efficiency: Templates can drastically improve the efficiency of manufacturing processes. Instead of starting from scratch or relying on memory, workers can follow a set procedure outlined in the template. This reduces the time spent on training, minimizes errors, and accelerates production timelines.
Documentation: Manufacturing templates often serve as a critical piece of documentation. They can be referred to when there’s a need to trace back production details or when there’s a requirement for audits and quality checks.
Scalability: As businesses grow, there’s a need to ramp up production without compromising on quality. Templates allow for quick scaling of operations. New employees can be onboarded faster, and production can be multiplied without significant hiccups.
Components of a Manufacturing Template
A comprehensive manufacturing template may include:
- Materials List: A detailed list of all raw materials and components required for production.
- Process Flow: A step-by-step guide to the entire manufacturing process, from start to finish.
- Machine & Equipment Details: Information on machinery and tools required, including their settings and operational guidelines.
- Quality Checks: Points in the process where quality checks should be conducted, including the criteria for acceptance or rejection.
- Safety Protocols: Guidelines to ensure the safety of workers, including the use of protective equipment and emergency procedures.
- Timeline: An estimated timeline for the production cycle, helping in planning and scheduling.
Importance in the Digital Age
In today’s digital era, manufacturing templates have evolved from paper-based checklists to sophisticated software solutions. Advanced Manufacturing Execution Systems (MES) and other industry-specific software now come with digital templates that can be easily customized, shared, and updated in real-time. These digital solutions offer analytics, real-time monitoring, and even predictive maintenance suggestions.
Moreover, with the rise of Industry 4.0, the integration of the Internet of Things (IoT) in manufacturing, templates are now more interactive. Machines can be programmed to follow templates autonomously, and any deviations or issues can be immediately flagged for human intervention.
In the ever-evolving landscape of manufacturing, templates remain a cornerstone for successful operations. They bridge the gap between human expertise and machine efficiency, ensuring that the end product is of high quality, produced efficiently, and meets the set standards. Whether you’re a small manufacturer or a global enterprise, the right template can be the difference between success and mediocrity in the competitive world of production.
6. Sample Manufacturing Value Stream Mapping Template
7. Sample Manufacturing Production Template
8. Sample Manufacturing Quality Control Checklist Template
9. Sample Risk Assessment in Manufacturing Template
10. Sample Root Cause Analysis of Manufacturing Template
11. Sample Manufacturing Information Sheet Template
12. Sample Manufacturing Fishbone Diagram Template
13. Sample Manufacturing Dashboards Template
Production vs. Manufacturing: Key Differences Explored
Production and manufacturing are two terms that are often used interchangeably. However, while they are closely related, there are distinct differences between the two. Understanding these differences is crucial for businesses and industry professionals to ensure they are applying the right strategies, tools, and methodologies for their operations.
1. Definition:
Production: Production is a broad term that refers to the entire process of creating goods and services. It encompasses a wide range of activities, from the extraction of raw materials and farming to the delivery of final products and services to consumers. Essentially, production can be seen as the overarching process of converting inputs (resources) into outputs (goods and services).
Manufacturing: Manufacturing is a subset of production. It specifically refers to the process of converting raw materials into finished goods through various processes, tools, machinery, and human effort. It involves activities such as machining, welding, assembling, and molding, to name a few.
2. Scope:
Production: The scope of production is broader and includes various sectors like agriculture, mining, construction, utilities, and more. It covers both tangible products like cars and intangible services like banking.
Manufacturing: Manufacturing’s scope is narrower, focusing solely on the creation of tangible goods. It doesn’t encompass service-oriented sectors or primary sectors like agriculture.
3. Processes Involved:
Production: Production processes can vary widely based on the industry. In agriculture, it might involve planting, nurturing, and harvesting crops. In the service industry, it could relate to tasks like consultation, training, or troubleshooting.
Manufacturing: Manufacturing processes are typically more standardized and involve specific steps to transform raw materials. Examples include casting, forging, milling, and 3D printing.
4. Value Addition:
Production: Production adds value at various stages, from raw material extraction to the provision of services. The value addition can be tangible or intangible.
Manufacturing: Manufacturing primarily focuses on adding tangible value by changing the physical properties of raw materials to produce finished goods.
5. Nature of Output:
Production: Production can result in both tangible products, like furniture or food items, and intangible services, like insurance or hospitality.
Manufacturing: The output from manufacturing is always a tangible product, like toys, electronics, or clothing.
6. Dependency:
Production: Production is a holistic term and doesn’t always depend on manufacturing. For example, service industries produce without engaging in traditional manufacturing.
Manufacturing: Manufacturing is inherently a part of the larger production system. Every manufacturing process contributes to the broader realm of production.
While both production and manufacturing are integral to the world’s economies, differentiating between the two is essential for clarity in business operations, strategy formulation, and academic discussions. In a nutshell, all manufacturing is production, but not all production is manufacturing. Recognizing this distinction helps in streamlining operations and setting clear objectives for businesses across various sectors.
14. Sample Manufacturing Action Plan Template
15. Sample Manufacturing Inspection Form Template
16. Sample Manufacturing Process Audit Template
Creating a Manufacturing Template: A Step-by-Step Guide
Creating a manufacturing template involves a systematic approach to standardize processes, ensure repeatability, and maintain product quality. Whether it’s for small-scale operations or a large factory setup, a well-crafted template can significantly enhance productivity and reduce errors. Here’s a step-by-step guide to creating an effective manufacturing template:
1. Define the Purpose:
Before you start, determine what the template aims to achieve. Are you looking to streamline a specific manufacturing process, improve quality control, or perhaps standardize safety procedures? Having a clear purpose will guide the development of the template.
2. Gather Information:
Research and gather all necessary data about the manufacturing process you’re focusing on. This could include:
Raw materials and their specifications
Machinery and equipment details
Operational steps and sequences
Quality benchmarks and standards
Time estimates for each step
3. Choose a Format:
Decide on a format that’s easy to follow and understand. Common formats include flowcharts, checklists, and step-by-step process guides. Nowadays, digital formats using software like Manufacturing Execution Systems (MES) or Enterprise Resource Planning (ERP) can offer interactive and real-time updating capabilities.
4. Break Down the Process:
Dissect the entire manufacturing procedure into clear, sequential steps. Be detailed in your descriptions, ensuring that even someone unfamiliar with the process can understand and follow it.
5. Incorporate Visual Elements:
Visual aids like diagrams, illustrations, and symbols can make the template more user-friendly. They provide clarity, especially for complex processes or when explaining machinery setups.
6. Highlight Safety Protocols:
Safety should be a priority in any manufacturing setting. Ensure that safety guidelines and precautions are prominently displayed within the template. This might include details about personal protective equipment, emergency shutdown procedures, and waste disposal guidelines.
7. Include Quality Check Points:
Determine stages within the process where quality checks are essential. Clearly mention the criteria for acceptance or rejection, tools required for the inspection, and any corrective measures to be taken in case of discrepancies.
8. Add Flexibility:
While standardization is the goal, flexibility is also essential. Include provisions or sample notes for adjustments, especially in cases where raw material specifications might vary or when using alternative equipment.
9. Review with Stakeholders:
Once the initial draft is ready, consult with relevant stakeholders such as process engineers, machine operators, quality control personnel, and even floor workers. Their feedback can offer valuable insights and help refine the template.
10. Test the Template:
Before full-scale implementation, test the template in real-time conditions. Monitor its effectiveness, check for any missed steps or ambiguities, and make necessary revisions.
11. Update Regularly:
Manufacturing processes and technologies evolve. To ensure that your template remains relevant and effective, schedule regular reviews and updates.
A robust manufacturing template not only standardizes operations but also becomes an invaluable tool for training, quality control, and process improvement. By investing time and effort into its creation, businesses can ensure a more streamlined, efficient, and error-free production environment.
Related Posts
Sample Business Card Templates
Sample Cashier Job Descriptions
Questionnaire Samples
FREE 10+ Sample HR Resource Templates in PDF
FREE 10+ HR Consulting Business Plan Samples in MS Word | Google Docs | Pages | PDF
FREE 49+ Sample Job Descriptions in PDF | MS Word
FREE 16+ Nonprofit Budget Samples in PDF | MS Word | Excel | Google Docs | Google Sheets | Numbers | Pages
FREE 13+ Academic Calendar Templates in Google Docs | MS Word | Pages | PDF
FREE 10+ How to Create an Executive Summary Samples in Google Docs | MS Word | Pages | PDF
FREE 23+ Sample Event Calendar Templates in PDF | MS Word | Google Docs | Apple Pages
Company Profile Samples
FREE 10+ Leadership Report Samples [ Development, Training, Camp ]
FREE 24+ Sample Payment Schedules in PDF | MS Word
FREE 10+ Return to Work Action Plan Samples in PDF | DOC
Autobiography Samples & Templates