Quality may be the most important thing to look for in any business or company on the planet. In any kind of business, the owner or manager always wants to reach a certain level of quality. It could be anything from the quality of products and services to the quality of the resources that are used to make them. Everyone makes sure that what they are making meets the expectations of their investors, stakeholders, and most importantly, their clients. With the need for high-quality products and services comes the responsibility to make sure that those quality standards are met. To make sure that what they make is good enough for the market, they do a lot of important things. There are a lot of things that need to be in place for these stages to go smoothly and for the best possible quality of their product to be consistently achieved. And good control plans are in charge of setting these parameters.
Planning is very important when it comes to making sure that the final product meets quality standards. It saves time and money by lessening the chance that items will be defective after they have been made. High-quality action plans are great at this, too. In addition to giving a clear picture of the high level of quality that the company or firm is trying to reach, it also lays out actions and rules that, when followed correctly, make sure that the end result is of the best possible quality. If you want to learn more about how a quality control plan works, look at the examples below to get a better idea of what it is and how to use it. You can also use them as a guide to help you write your own control plan.
6+ Design Quality Control Plan Samples
1. Design Quality Control Plan
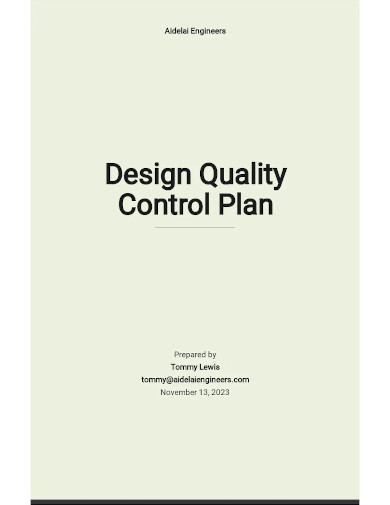
2. Sample Design Quality Control Plan
3. Highway Safety and Design Quality Control Plan
4. Construction Quality Control Plan
5. Simple Quality Control Plan
6. Quality Control Plan for Water Project
7. Design Quality Control Plan Example
What Is a Design Quality Control Plan?
It’s usually the last thing a company does before putting something out into the world. To make sure that the goods meet quality standards, producers perform a variety of tasks, such as quality checks and corrections, at this point in the process.
If the product is ready to be shipped to the customer, this is a very important step. A bad reputation, less customer retention, and more returns could happen if you don’t deliver high-quality goods.
Also, quality control looks at how a product is made, stored, and distributed. People use the term “defective” when something isn’t good enough or broken. As a result, businesses need to build efficient systems that keep their products safe through all stages of the supply chain.
On the basis of the type of business and the types of products that a company sells, it may be necessary to use both internal and external quality control measures. An example of internal control can be found in businesses that have their own rules. This could be anything from fixing equipment to looking at how well employees are doing and everything else in between. Upper-level managers are in charge of making sure that quality assurance procedures are done the right way and at the right time.
External quality control, on the other hand, is important for products that are sold to other people. For example, after food is made and distributed, outside businesses must check the product to make sure it is healthy and hasn’t gone bad before it can be sold in the market.
QCP stands for Quality Control Plan, and it is a written list of procedures and actions that are meant to make sure that the goods that are made for a project meet the quality standards that were set out in the contract and in other procedures and manuals, as well as in other guidance.
How To Write a Design Quality Control Plan
1. Create an organization chart
Organizing a chart of jobs, qualifications, and training for each quality assurance method is the first step that management should take to make sure everything is set up the right way. These standards must be written down to show that the people who do inspections are properly trained and competent. This document should be kept on file so that it can be shown to senior management if there is a problem or an error. This way, they can see what happened.
2. Define responsibilities
Following that, management needs to make sure everyone knows what their roles are inside and outside the company. Each partner should know what they are responsible for and who will be in charge of making sure their work is good. While some small businesses let employees check the quality of their own work, most businesses require that these procedures be done by a different group of people. This means that separate documents need to be made to make sure that each project was given enough time, as multitasking could lead to more mistakes. Large companies, on the other hand, prefer that different people in the same department check the work of their coworkers. These quality assurance specifications should be very clear to avoid confusion and to make sure that each step is done as detailed as possible.
3. Purchase and receive materials
Before ordering materials, management should make sure they understand the specifications. This way, they can be sure that the parts they buy meet the quality standards they want. To save money, some businesses try to find vendors who charge the least. In the long run, this could make them fall short of their quality assurance standards. As a result, before you start the ordering process, it is important to figure out what the important qualities of the materials are. The materials have been delivered, and now that they are there, staff should check the shipment to make sure that all of the products meet the standards. It’s up to the company to return the items to the supplier if they don’t meet their standards.
4. Verify Suppliers’ Qualifications
While it’s easy to check basic materials, it can take a long time and be difficult to check more complicated parts and equipment for quality. Companies should be clear about what they want from vendors before they send out a bid request. Businesses, for example, could ask for a third-party audit of a vendor to make sure their internal processes are in line with the rules. As a result, before making a deal, businesses should check the supplier’s reputation. They should also check their brand and their qualifications.
5. Evaluate Quality Feedback
It is the job of quality assurance to make sure that the products are up to standard before they are sold to customers. However, feedback is a great way to improve a product’s performance as well as improve its overall quality. Companies can figure out how good and bad a product is by looking at online reviews, user complaints, and ideas from other customers. If you run a business, you should have a customer care team that looks at evaluations and compliance records to see if problems were caused by non-compliance. If an employee finds out that a process is not in line with the law, they must report it.
6. Develop a Process for Corrective Action
Finally, companies need to come up with a plan to fix problems with quality, like breaking the law or not following the rules. When a non-compliant process is reported, the person in charge of quality control must look into what happened. It could be because of a mistake or because an employee didn’t do their job. A preventative measure must be put in place after the root cause of the problem has been found. This will keep the same thing from happening again. In this package, there could be extra quality checks or automated tools, like inventory ordering systems, that could be used. If a product is recalled or there are other problems with it, quality control plans help businesses make sure that the correct steps are in place to fix the problem. This shows to customers that a company cares about them and wants to make the best products on the market.
FAQs
What are the three types of quality?
A lot of professionals break down quality defects into three groups: minor flaws, major flaws, and critical flaws. Minor flaws are those that make up less than one percent of the whole. Defects are put into groups based on the nature and severity of them.
What are action steps?
Action steps are the specific things you do to reach the goals you set out in your action plan. It’s what you write in your action plan that makes up the whole thing, so that’s what it’s about.
What are the four types of quality control?
Process Control. Control Charts. Product Quality Control. Process Control.
A well-written action plan guarantees that the objectives of your business or corporation, or even your own personal objectives, are met and exceeded. To put it another way, it brings your vision to life. It can assist you in maintaining the proper course for your project and avoiding any potential complications that may arise in the process. It’s essentially the same process for creating a high-quality action plan. It helps you maintain a particular level of quality in your products and services while also ensuring that you have room for continuous improvement.
Related Posts
FREE 9+ 30-Day Marketing Plan Samples in PDF | MS Word | Apple Pages | Google Docs
FREE 3+ Sales Team Action Plan Samples in PDF | MS Word | Apple Pages | Google Docs
Marketing Plan For Small Business Samples
FREE 7+ Fashion Business Plan Samples in PDF
FREE 10+ Sprint Planning Samples In MS Word | Google Docs | PDF
FREE 10+ Wedding Planning Samples in MS Word | Apple Pages | Powerpoint | PDF
FREE 9+ Monthly Study Planner Samples in PSD | Illustrator | InDesign | PDF
FREE 9+ Sample Curriculum Planning Templates in PDF | MS Word
FREE 10+ Teacher Development Plan Samples in MS Word | Google Docs | Apple Pages | PDF
FREE 10+ Basketball Practice Plan Samples in PDF
FREE 12+ School Business Plan Samples in PDF | MS Word | Apple Pages | Google Docs
FREE 7+ Client Strategic Plan Samples in PDF | MS Word
FREE 11+ Trucking Business Plan Templates in PDF | MS Word | Google Docs | Pages
FREE 7+ Small Hotel Business Plan Samples PDF | MS Word | Apple Pages | Google Docs
FREE 14+ Bakery Business Plans in MS Word | PDF | Google Docs | Pages