What do in demand engineering and manufacturing firms have in common? Well, the answer is quality work and products that are created following accepted standards. Providing quality service is never easy no matter what industry they belong. It goes to show how strict and effective their internal auditing department in issuing non-conformance reports. It’s basically the reason why top rated firms offer the best services. In this article, we will touch on the basics of non-conformance reports. The report samples provided below will also help us familiarize the document’s format.
FREE 10+ Non Conformance Report Samples
1. Product Non-Conformance Report Template
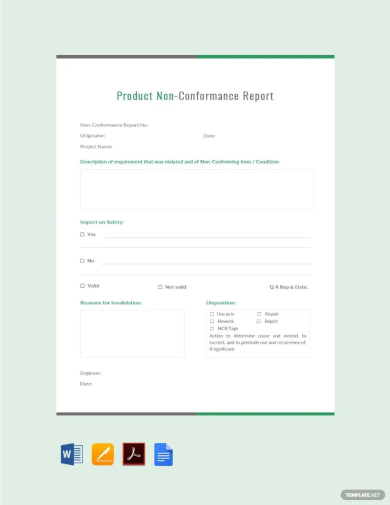
2. Sample Supplier Non Conformance Report Template
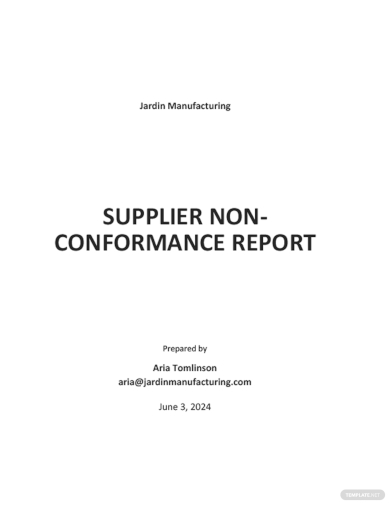
3. Audit Non Conformance Report Template
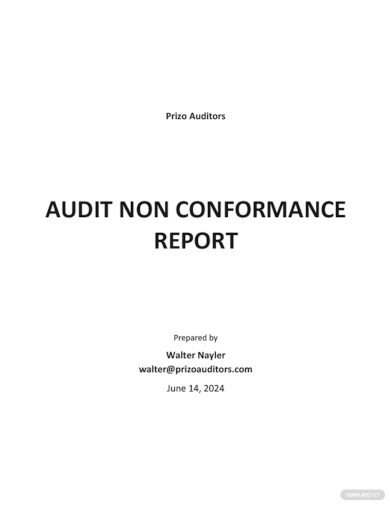
4. Free Simple Non-Conformance Report Template
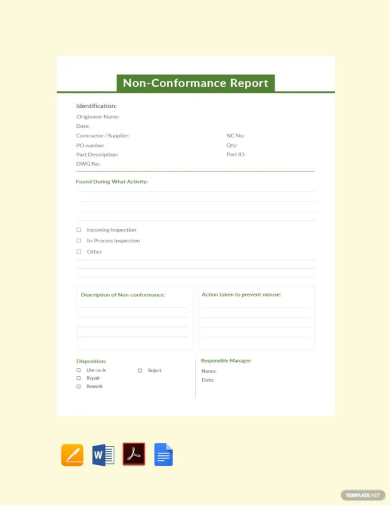
5. Free Project Non-Conformance Report Template
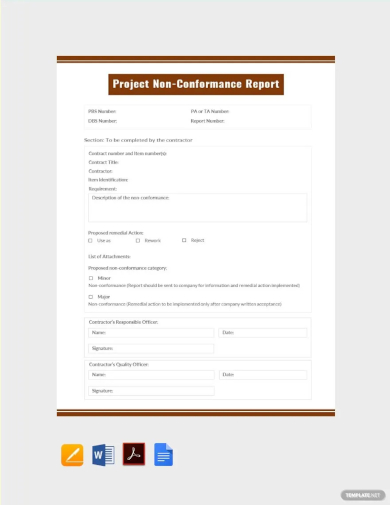
6. Free Process Non-Conformance Report Template
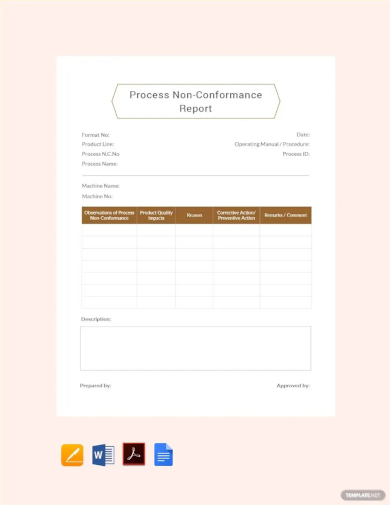
7. Free Manufacturing Non-Conformance Report Template
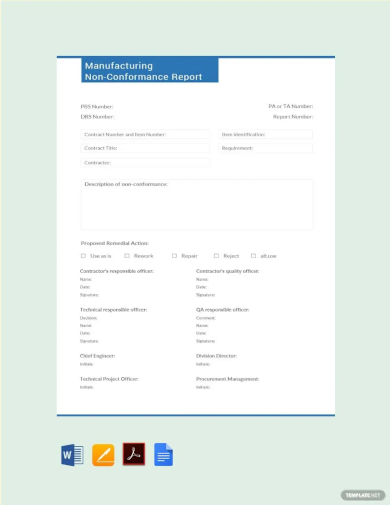
8. Free Customer Non-Conformance Report Template
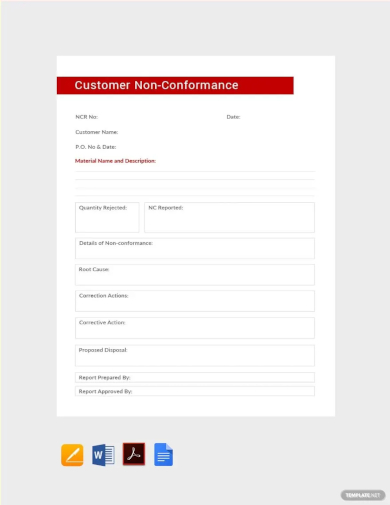
9. Non Conformance Report Template
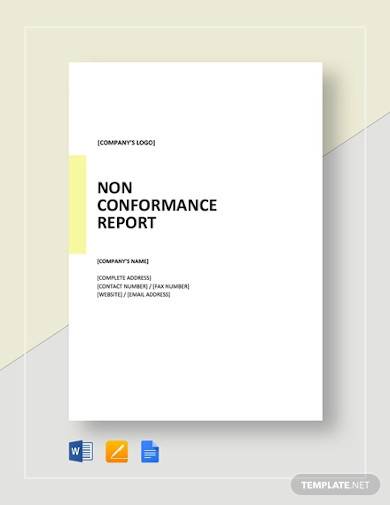
10. Sample Non-Conformance Report Template
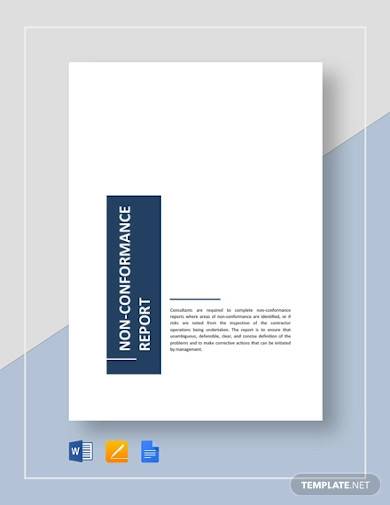
11. Sample Non Conformance Report Template
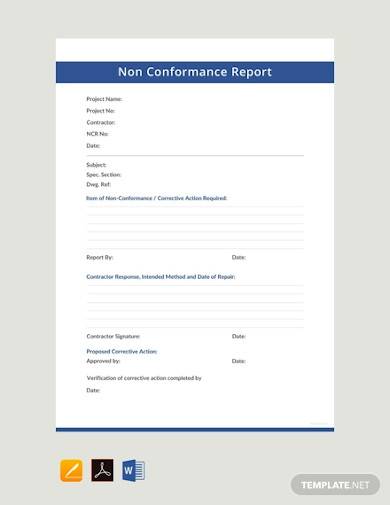
12. Free Non conformance Report Template
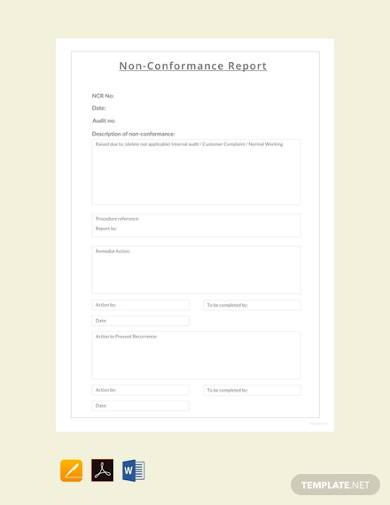
13. Quality Non conformance Report Template
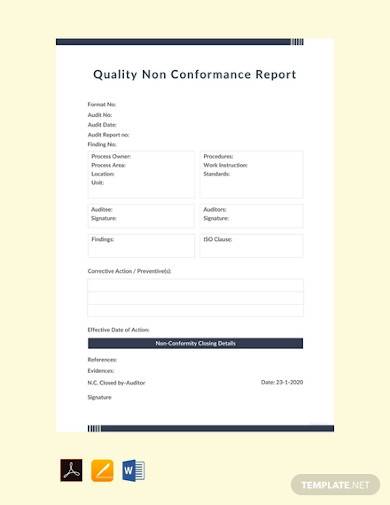
14. Basic Non-Conformance Report Template
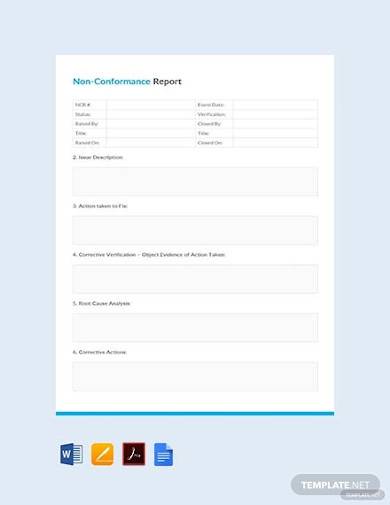
15. Non Conformance Report Format
16. Non Conformance Report Form Template
17. Blank Non Conformance Report Template
18. Non Conformance Report Form Template
19. Simple Non Conformance Report Template
What Is a Non-Conformance Report?
A non-conformance report is a construction-related report that is used to address specific deviations from work that does not meet quality standards. Further problems with construction and manufacturing are prevented when a non-conformance report is issued. It can be likened to a quality audit report, project audit report, or an internal audit report. Issuance of the report means that quality standards are not followed, and immediate action is necessary. A non-conformance report includes the details of the identified problem; where, when, and how it occurred; and who is responsible for the issue.
How To Make a Non-Conformance Report
You can say that a non-conformance report is the opposite of a compliance report. With that, you’ll probably have an idea of the information to put into your report. Here is a typical flow of a non-conformance report that you can use as your guide.
1. Identification of Process/Product Failure
The start of the problem is identified when there are flaws to a product or when and a particular process fails and causes other related methods to fail. This instance must be reported promptly so that further damage can still be contained.
2. Report Documentation
The identified issue merits a non-conformance report. The report template will provide details related to the incident or the non-conformance. It answers the 4Ws (who, what, where, when) and how of the non-conformance activity that occurred.
3. Project Investigation
The management will be conducting a high-level investigation after studying the report. A root cause report analysis will also be undertaken to attempt to find the real cause of the reported issue.
4. Initiation of Corrective Action
The team will need to find an immediate but effective solution to the problem. They’ll need to come up with an acceptable action plan that will correct the problem and prevent it from recurring.
5. Resolution and Mitigation
The final step deals with ensuring that the problem is completely resolved and that the same mistakes won’t happen again. The team will need to ensure that the problem’s recurrence is mitigated if not eliminated.
FAQs
When is a non-conformance report issued?
A non-conformance report is all about the quality of the work provided. Work that is done according to standards will not merit a non-conformance report. So when a non-conformance report is issued, it means that the following deviations from the standards have taken place:
- The inspection team has identified quality defects because the team failed to follow the approved or standard operating procedure.
- The design does not represent the actual conditions in the field.
- Provided inaccurate construction designs review.
- Use of substandard or unapproved materials as a substitute.
- Products tested do not meet quality established standards.
- The testing and inspection plan was not followed.
- Putting the safety of workers at risk.
- Using unapproved methods or standards for work.
- Did not meet construction tolerances specified in the project scope.
- Work is not done, as indicated in the drawings/designs.
Who can issue a non-conformance report?
There is no specific rule as to who can issue a non-conformance report unless an organization or a team designates someone for the task. Any member of the project work team can issue a non-conformance report. The report must consist of facts and sufficient backup information for the non-conformance claims. After a non-conformance report is issued, corrective actions are performed before the issue considered closed.
What should you include in a non-conformance report?
Here are some of the information that you should include in a non-conformance report:
- Statement of the non-compliance
- Project name
- Team name/Department
- Name of auditor for internal audit
- Work standards (instructions, procedure, manufacturing process, company policies, documented social norm, organizational ethics)
- Identified non-compliance violations
- Location/setting
- Time and date/incidences
- Objective evidence/Physical evidence of non-compliance
What is the proper way of responding to a non-conformance report?
If you received a non-conformance report, you’d need to address it as soon as possible. However, you cannot just do what you think is right. The steps to appropriately respond to a non-conformance report are listed below:
- Discuss matters with the person who issued the report.
- Prepare the implementation of the corrective action plan necessary to fix the identified problem.
- After implementation, get your work inspected to ensure that the issue is adequately solved.
- Send a formal letter explaining why the non-conformance report was issued and the corrective actions are taken to fix the problem and prevent a recurrence.
- Ensure that your team approves of the action plan you’ve created.
Doing honest work and following established standards will not merit a non-conformance report. It is important to detect issues with compliance early to ensure the quality of work evaluation, regardless of its nature. If you need to issue such a report, then you can use the downloadable samples in this article as your guide.
Related Posts
FREE 13+ Sample Quality Manuals in PDF
FREE 11+ Sample Construction Worker Resume Templates in MS ...
FREE 10+ Consultant Scope of Work Samples in PDF MS Word
FREE 9+ Software Test Plan Templates in PDF MS Word
FREE 10+ Environmental Management Plan Samples in PDF MS ...
FREE 9+ Certificate Samples in MS Word
FREE 12+ Sample Medical Certificate for Sick Leaves in MS Word ...
FREE 7+ Sample Project Manual Templates in PDF
FREE 25+ Sample Certificate of Compliance in PDF PSD | AI ...
FREE 13+ Sample Medical Certificate for School in MS Word PDF
FREE 9+ Athletic Director Job Description Samples in MS Word PDF
FREE 9+ Sample Welder Job Description Templates in MS Word PDF
FREE 12+ Scope Statement Templates in PDF MS Word
FREE 9+ Medical Examiner Job Description Samples in MS Word ...
FREE 15+ Construction Contract Templates in PDF Google Docs ...