Six Sigma is a management philosophy that emphasizes statistical improvements to a company process and emphasizes qualitative success assessments above qualitative indicators. As a result, Six Sigma practitioners are businesspeople who increase business functionality through the use of statistics, financial analysis, and project management. Six Sigma is a statistical metric that demonstrates how well a business process functions. As previously stated, an error arises when an event deviates six standard deviations from the mean and occurs less than 3.4 times per million events. This means that if a process produces fewer than 3.4 mistakes per million chances, it is deemed efficient. Anything created that does not meet the expectations of the customer is referred to as a fault.
10+ Six Sigma Samples
Six Sigma is a set of management tools and procedures aimed at lowering the likelihood of errors in the workplace. It is a data-driven approach to defect elimination that employs a statistical methodology. The Greek sign “sigma”, a statistical term for quantifying process variation from the process mean or target, is used in the etymology. The term “Six Sigma” comes from the statistical bell curve, where one Sigma represents a single standard deviation from the mean. The fault rate is rated as “very low” if the system has six Sigmas, three above and three below the mean.
1. Lean Six Sigma Business Plan
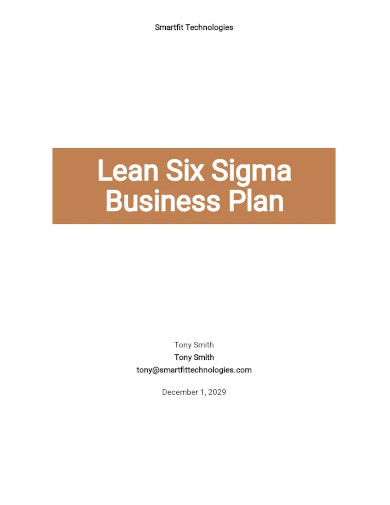
2. Lean Six Sigma
3. Six Sigma Green Belt
4. Six Sigma Zone
5. Six Sigma White Belt Training
6. Sample Six Sigma
7. Simple Six Sigma
8. Basic Six Sigma
9. Digital Six Sigma
10. Rapid Six Sigma
11. IT Six Sigma
Principles of Six Sigma
- Focus on the customer – The fundamental purpose is to provide maximum advantage to the consumer, which is based on the widespread notion that “the customer is king.” To do so, a company must first understand its customers, their wants, and what motivates them to buy or stay loyal. This necessitates developing a quality standard based on what the consumer or market needs.
- Measure the value stream and find your problem – To identify waste regions, map the processes in a given process. Gather information to identify the exact issue that needs to be addressed or modified. Establish specific data collecting goals, such as specifying the data to be collected, the reason for the data collection, the expected insights, guaranteeing measurement accuracy, and building a standardized data collection system. Determine whether the data is assisting in the achievement of the objectives, and whether the data needs to be refined or new information obtained. Determine the issue. Ask questions to get to the bottom of the problem.
- Get rid of the junk – Once the problem has been recognized, alter the process to eliminate variation and consequently problems. Remove any steps in the process that do not bring value to the client. If the value stream fails to identify the source of the problem, tools are employed to find outliers and trouble areas. To achieve quality control and efficiency, streamline functions. Finally, by removing the aforementioned garbage, bottlenecks in the process are eliminated.
- Keep the ball rolling – All parties should be involved. Adopt a structured approach for problem-solving in which your team contributes and collaborates on their various areas of expertise. Because Six Sigma procedures can have a significant impact on a business, the team must be well-versed in the principles and methodology employed. To limit the risk of project or re-design errors and make sure that the business runs smoothly, specialist training and knowledge are necessary.
- Ensure a flexible and responsive ecosystem – Business transformation and change are at the heart of Six Sigma. When a flawed or inefficient process is eliminated, it necessitates a shift in work practices and employee attitudes. A strong culture of flexibility and openness to changes in procedures can help ensure that projects are completed quickly and efficiently. People and departments involved should be able to adapt to change quickly and seamlessly, thus processes should be built to assist this. Finally, a competitive advantage can be gained by a company that keeps an eye on the data, evaluates the bottom line on a regular basis, and adapts its operations as needed.
FAQs
What are the five steps of six sigma?
- A group of individuals, led by a Six Sigma champion, decides on a broken process to focus on, based on an examination of the company’s goals and requirements. This definition explains the project’s problem, objectives, and deliverables.
- The team assesses the process’s first performance. These statistical indicators assist the team analyze the process’s benchmark performance and create a list of potential inputs that could cause the problem.
- The team then evaluates the process by isolating each input, or potential cause of failure, and putting it to the test as the source of the issue. The team employs analytics to determine the source of process errors.
- From then, the team strives to improve the system’s performance.
- To ensure that the process does not regress and then become unproductive again, the group adds controls to it.
What is lean six sigma?
Lean Six Sigma is a team-oriented management technique that aims to increase performance by reducing waste and faults while increasing job uniformity. It integrates Six Sigma methodology and tools with the lean manufacturing-lean enterprise mindset, with the goal of reducing waste of physical resources, time, effort, and talent in production and organizational processes while maintaining quality. Any resource utilization that does not add value to the end consumer is wasteful and should be eliminated.
Six Sigma certification can be obtained through a corporation or a college. Keep in mind, however, that the curriculum is not standardized by any unified authority. This means that courses can differ depending on where you take them.
Related Posts
Sample Business Card Templates
Sample Cashier Job Descriptions
Questionnaire Samples
FREE 10+ Sample HR Resource Templates in PDF
FREE 10+ HR Consulting Business Plan Samples in MS Word | Google Docs | Pages | PDF
FREE 49+ Sample Job Descriptions in PDF | MS Word
FREE 16+ Nonprofit Budget Samples in PDF | MS Word | Excel | Google Docs | Google Sheets | Numbers | Pages
FREE 13+ Academic Calendar Templates in Google Docs | MS Word | Pages | PDF
FREE 10+ How to Create an Executive Summary Samples in Google Docs | MS Word | Pages | PDF
FREE 23+ Sample Event Calendar Templates in PDF | MS Word | Google Docs | Apple Pages
Company Profile Samples
FREE 10+ Leadership Report Samples [ Development, Training, Camp ]
FREE 24+ Sample Payment Schedules in PDF | MS Word
FREE 10+ Return to Work Action Plan Samples in PDF | DOC
Autobiography Samples & Templates