Work orders are vital to the success of maintenance and construction workers. A good work order lays out the job or task needed and provides all of the needed information to get the job done. Work orders are the foundation of successful maintenance management. Not only are they simple tools for scheduling and assigning job tasks, but they also help monitor the variety of resources spent on maintenance. Work orders are important because they play an essential part in standardizing maintenance workflows, particularly that of submitting work requests to closing work orders. This article will guide you on how to make a subcontractor work order
10+ Subcontractor Work Order Samples
1. Subcontractor Work Order Agreement Template
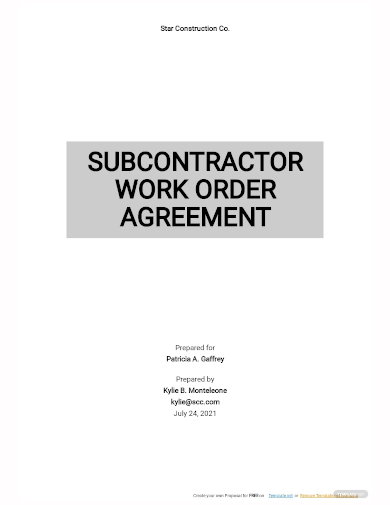
2. Subcontractor Work Order
3. Company Subcontractor Work Order
4. Laboratory Subcontractor Work Order Form
5. Annual Subcontractor Work Order Agreement
6. Dental Laboratory Subcontractor Work Order Form
7. New Subcontractor Work Order
8. Sample Subcontractor Work Order
9. Management Subcontractor Work Order Agreement
10. Subcontractor Contract Work Order
11. Master Subcontractor Work Order Agreement
What is a Work Order?
A work order is a formal written communication that authorizes a maintenance team or other member of field engineering to complete a job or task for a customer. Work orders encompass an array of requests including repair or replacement. A work order indicates a job or task has been approved and is ready to go into the queue for completion. Work orders can be transmitted electronically or on paper.
How to Write a Work Order – Step by Step
Writing a work order can seem like a daunting process. Making sure that all the information needed to correctly tackle a problem is the most vital part of the process. Here simple step-by-step procedure that you can take to accurately construct a flawless work order:
Step One: Identify the Problem
The first step to writing any work order is to identify the work that needs to be done. Be sure to include specifics about the location where the task or job needs completed, how long the problem has been going on for, and any special skills or tools that are needed to complete the work. It’s also vital to identify whether or not the task requested is an emergency at this stage.
Step Two: Document the Specifics
A key aspect of a good work order includes specific details about the request. It’s important to ensure these details are a part of the work order:
- Name and contact number of the requestor and creator
- Date and time the requested issue first occurred and when the work order was requested
- Estimated cost for repairs and time of completion
- Outline of how modifications in the scope of work will be communicated
Step Three: Assign the Work Order
Format your information in a way that is easy to read and assign the work order to the best maintenance technician for the job.
FAQs
What are the details to include in a subcontractor work order?
- A detailed description of the job, including the location.
- The name and contact information for the entity requesting the work.
- An overview of any special circumstances that contribute to completing the job efficiently and correctly.
- A detailed account of any specific problems that need to be repaired.
- An estimated time of job or task completion.
- The name of the maintenance person completing the job or task.
- A list of any required parts, tools, or knowledge required to complete the job.
- An estimate of any costs that might be incurred.
What are the different types of work orders?
Work orders apply to many different types of requests and categories. Depending on the property the maintenance is requested on and the types of work needed, many sub-categories can apply to work orders.
Here are some examples of the most common types of work orders:
- Inspection : Inspection work orders entail a highly-skilled professional testing out an asset or system. This function is completed to ensure that all components of a system or asset are working as expected.
- Emergency : Emergency work orders apply when a job or task request threatens the life or well-being of inhabitants or assets. In extreme cases, a work order may not be generated in favor of getting the job done as quickly as possible.
- Safety : A safety work order exists to protect the well-being of inhabitants of a structure. These types of work orders include scenarios such making repairing dangerous damages or cleaning up hazardous materials at a facility.
- Preventative Maintenance : Much like changing the oil in your car or replacing air conditioner filters, preventative maintenance work orders aim to solve problems before they arise. These work orders can include tasks ranging anywhere from routine cleaning to equipment tune-ups and more.
- Electrical : Electrical maintenance focuses on servicing any electrical parts of a facility. This could entail changing a light bulb or performing service on a faulty breaker box.
- Special Projects : Not all work order requests can be filed away neatly into a specific category. There are numerous miscellaneous requests that a work order can help fill, as well. These might include upgrading equipment or replacing outdated software.
What is a work order cycle?
Every maintenance work order has a lifecycle with three main phases – creation, completion, and recording. These phases can be broken down into six steps, including task identification, requesting a work order, scheduling the work order, assigning and completing the work order, documenting and closing the work order, and analyzing the work order to help improve the process for next time. Understanding each step and having a solid work order process ensures tasks don’t get stuck in one phase and turn into backlog.
Related Posts
Sample Business Card Templates
Sample Cashier Job Descriptions
Questionnaire Samples
FREE 10+ Sample HR Resource Templates in PDF
FREE 10+ HR Consulting Business Plan Samples in MS Word | Google Docs | Pages | PDF
FREE 49+ Sample Job Descriptions in PDF | MS Word
FREE 16+ Nonprofit Budget Samples in PDF | MS Word | Excel | Google Docs | Google Sheets | Numbers | Pages
FREE 13+ Academic Calendar Templates in Google Docs | MS Word | Pages | PDF
FREE 10+ How to Create an Executive Summary Samples in Google Docs | MS Word | Pages | PDF
FREE 23+ Sample Event Calendar Templates in PDF | MS Word | Google Docs | Apple Pages
Company Profile Samples
FREE 10+ Leadership Report Samples [ Development, Training, Camp ]
FREE 24+ Sample Payment Schedules in PDF | MS Word
FREE 10+ Return to Work Action Plan Samples in PDF | DOC
Autobiography Samples & Templates